A systematic find out about by means of Dr.-Ing. Marijke van der Meer (Krebs & Riedel Schleifscheibenfabrik GmbH & Co. KG) presentations that by means of adjusting sprucing parameters equivalent to power, velocity, and grain measurement, the lifespan of double disc grinding wheels and sprucing gear may also be considerably prolonged. This makes a regular sprucing procedure much less high quality and advocates for a centered adjustment to the precise necessities of the software. Technological consulting and optimization on the buyer’s web page can undoubtedly affect the cost-effectiveness and potency in double disc grinding with planetary kinematics.
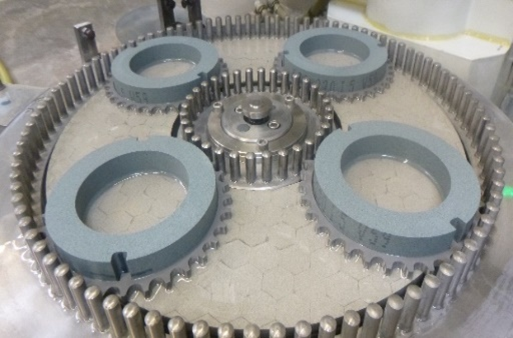
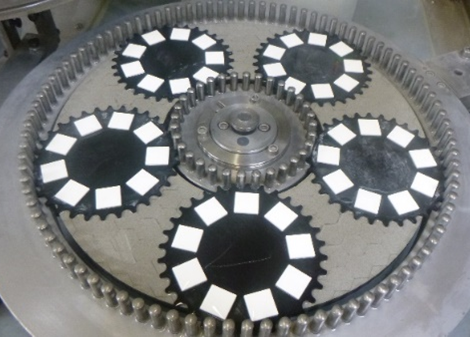
Prerequisites and Parameters all over Polishing:
A check device from Mµtech, type AC500F, used to be used. This has been particularly tailored for Krebs & Riedel to house smaller software diameters to stay checking out prices low. To verify reproducible sprucing stipulations, the damage of the sprucing ring is recorded, documented, and no less than one repetition is carried out. The coolant used is the emulsion Syntilo 81 E (5.4%). Polishing rings are immersed or wetted in it, whilst no coolant is equipped all over the sprucing procedure. Therefore, the grinding wheels are wiped clean.
In the usual sprucing process, one facet is sharpened concavely and as soon as convexly to stay the wheels instantly. Simplest the rotation course of the interior pin ring adjustments. The speeds in revolutions in line with minute (rpm) are: concave: nmost sensible 30 / nbackside -36 / ncenter -24 and convex: nmost sensible 30 / nbackside -36 / ncenter 24. The primary load pressure is 38 daN, and the sprucing time in line with rotation course is 25 seconds, with the primary 5 seconds devoted to wetting with coolant. Put on from each the sprucing ring and decrease grinding wheel is recorded – the latter after each sprucing and grinding.
To start with, grinding wheels with specs 4D 76 X 18 V8318-40 and closed structure are tested, that are sharpened with 57C 220 I 5 V59 (Determine 1). For dulling, parts produced from aluminum oxide ceramic (Determine 2) are processed. Right here, 9 parts measuring 20 x 20 mm² from ALOTEC92 in line with service with 5 carriers correspond to a subject matter structure of twenty-two.4%. The primary load speeds are nmost sensible 200; nbackside -200; ncenter 20 rpm with a beginning grinding pressure in major load of 30 daN. The removing price is ready at 100 µm/min with an infeed in line with run of 200 µm. The grinding pressure will increase robotically when dulling the grinding wheels to take care of removing price. Runs proceed till a most pressure of 250 daN is reached to verify uniform dulling of the grinding floor.
In every trial, procedure cycle occasions, forces, precise removing charges, and put on on grinding wheels are documented. For aluminum oxide plates, roughness essentially arises from coarse subject matter construction and is impartial of sharpness stage; thus, analysis of part roughnesses is left out right here. Even with a lifeless software, a Ra > 0.5 µm and Rz > 5 µm are accomplished.
To seize sharpness ranges below more than a few procedure diversifications, one way the usage of graphite imprints has been presented. Maintaining gadgets for graphite items had been created the usage of 3D printing. Those graphite items constitute the produced envelope curve of grinding wheel topography as roughness when processed by means of higher and decrease discs.
Effects
To start with ranging from the described usual sprucing procedure, power used to be numerous. Upper power does no longer robotically imply sharper discs in line with roughness measurements; that is showed by means of subject matter removing on graphite (Determine 3).
The values in Determine 4 had been recorded all over roughness size of graphite; it will have to be famous that graphite prints correspond to a damaging influence of overlaid grinding wheel topography. This implies Rvk represents grain guidelines whilst Rpk represents topographic valleys (pores/chip house). Rpk and Rvk illustrate that extra dulling happens externally than internally; thus, the middle of the chopping software ring turns into maximum flattened. The highest facet stays quite sharper than the ground facet.
After sprucing, surfaces are all the time distinctly rougher than after grinding; Rvk presentations much less distinction between sprucing and grinding in comparison to Rpk the place grains (Rvk) put on not up to the bond (Rpk).
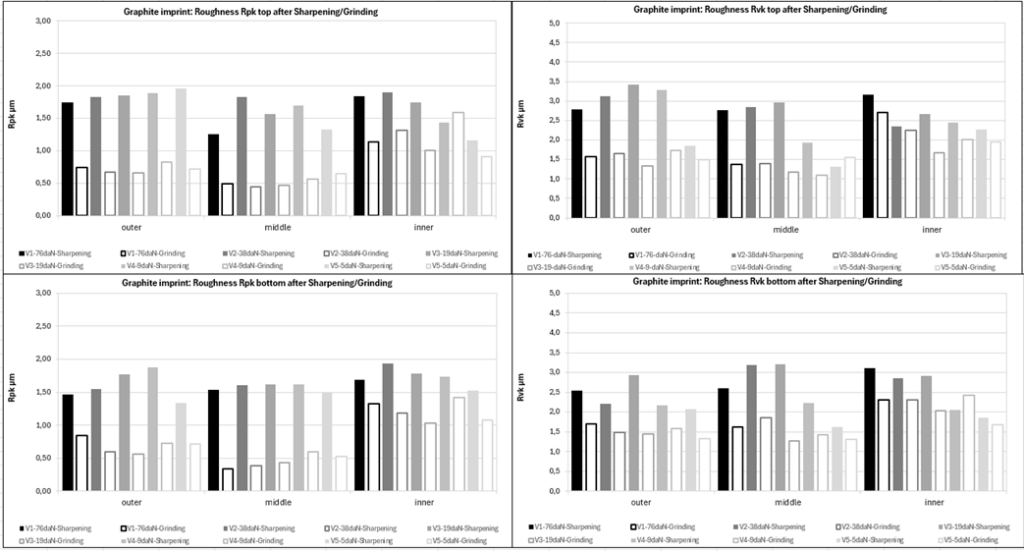
Relating to general subject matter removing peak, there are minimum variations in grinding processes following power variation all over sprucing; then again, relating to software put on there’s an observable distinction more than an element of 3 (Determine 5).
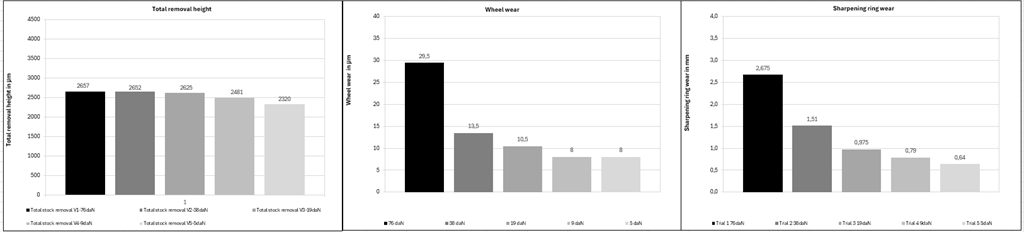
Usually, put on quantity of discs VS in mm³ is when compared towards general quantity VW in mm³ flooring from workpieces to judge procedure potency by the use of what’s referred to as G-value. Prime G-values point out lengthy software lifestyles:
Right here disc put on happens extra all over sprucing processes whilst bearing in mind that sharp rings will have to even be accounted for as “consumables.” Thus, an potency price E is presented derived from evaluating general removing quantity VW towards sum volumes of disc put on VS plus sharp ring put on VSR:
But even so power changes had been additionally made to speeds in addition to grain sizes all over sprucing processes -reducing each power and velocity undoubtedly affects potency whilst best important adjustments in grain measurement yield results.
This adjustment without delay influences imaginable rate numbers regarding a collection of grinding wheels (assuming a coating thickness of six mm) in addition to required selection of sharp rings all the way through disc lifespan.
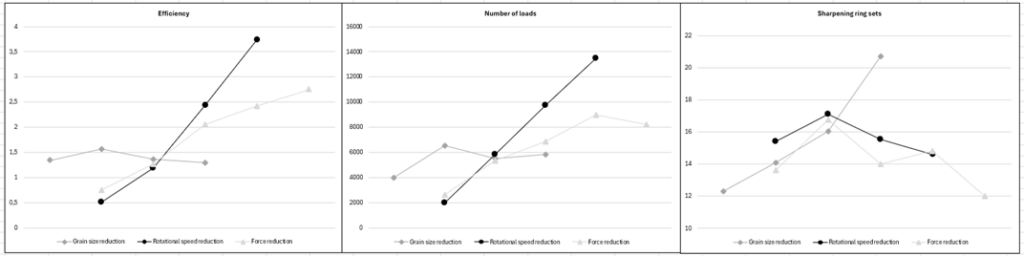
Decreasing power along speeds results in stepped forward potency inside each sprucing and grinding processes – the investigation published that power higher software put on by means of greater than an element of 3.
Effects indicated that reducing pressures at the side of speeds complements procedure potency whilst adjustments in grain measurement best had important results below robust deviations -these changes without delay influenced lifespan for units of grinding wheels at the side of quantity wanted for sharp rings.
In abstract for optimum potency in double-disc high quality grinding it’s beneficial no longer simply to take care of usual processes but in addition put in force centered changes on procedure parameters like power or velocity to increase software lifestyles whilst bettering general procedure potency.
Krebs & Riedel makes a speciality of processing brittle onerous fabrics equivalent to glass & sapphire ceramics (SiC & SiN), blended ceramics & onerous metals at the side of metal & steel alloys processing too.
Krebs & Riedel has additionally advanced new high quality grain specs for massive floor space grinding inside nanometer vary that includes top removing charges – the corporate provides adapted sprucing rings along international technological toughen geared toward optimizing buyer software potency & longevity.
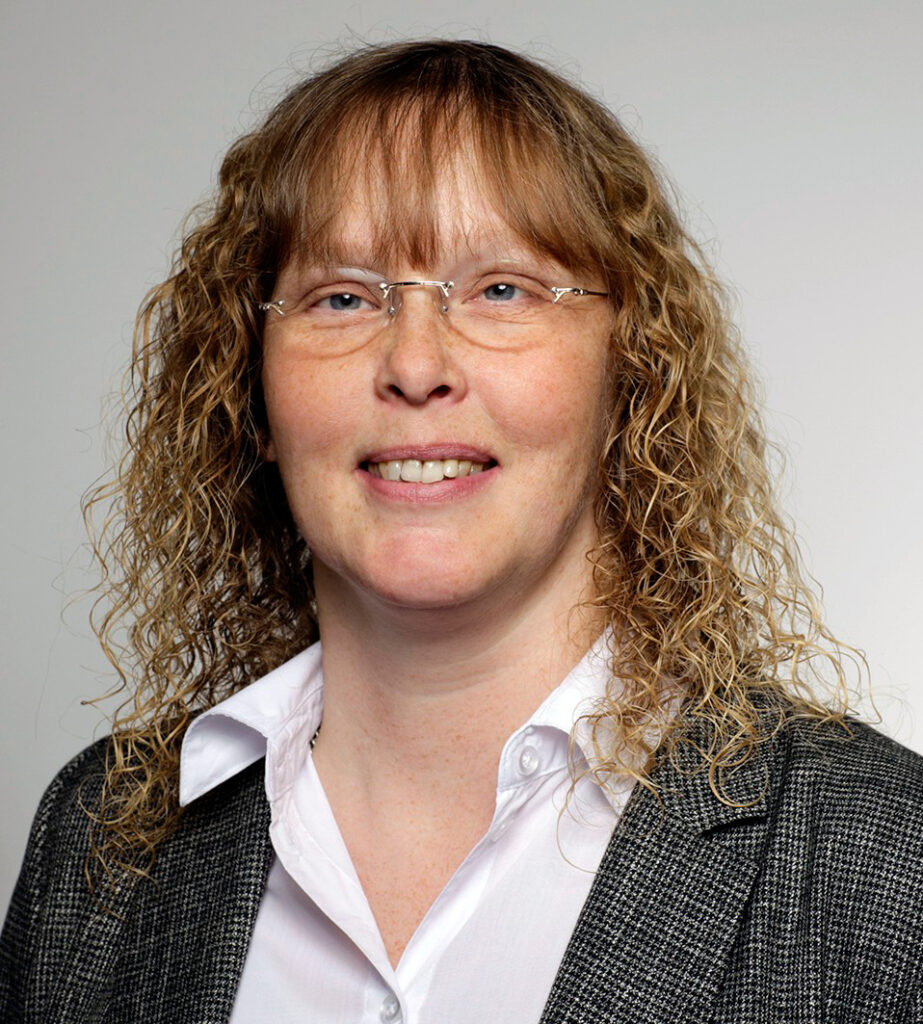
Dr.-Ing. Marijke van der Meer
Analysis & Building
m.vandermeer@krebs-riedel.de